Eye On Equipment
Processing Children's
Eyewear
By Susan P. Tarrant
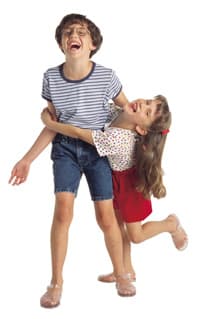
Equipment vendors are working hard to make sure their technology keeps pace with the advancements of lens materials. Edging equipment today is able to easily handle most, if not all, of the lens materials a dispenser can throw at it.
However, sometimes the equipment is required to process special lenses or deal with unusual situations.
In order to help dispensers solve the next challenging quandaries, we asked industry equipment experts' advice on working with children's eyewear and the lens materials most frequently prescribed for it, polycarbonate and Trivex.
Problem
I seem to have a relatively high percentage of spoilage due to scratching with children's eyewear, how can we improve?
Solution
There are several variables that generally make children's eyewear more difficult from the processing point of view. Safety is a priority. Cosmetically speaking, you want to do everything possible to make children's eyewear as thin and light as possible. And, obviously, the frame size is going to be smaller.
Generally, polycarbonate is the material of choice. That in itself isn't such a challenge, but handling the lenses and minimizing the opportunity for scratching can be.
With children's eyewear, there is less surface area to actually hold the lens, so you are more apt to put your fingers in critical areas when safety beveling or inserting the lenses in the frame.
One way to minimize exposure is to use surface saver dots on both sides of the lens. This will not pose a problem unless the material extends out to the edge of the lens.
If it does, you may have bevel placement issues. Simply trim the material before applying.
Another way to eliminate the risk factor would be to use an edger that automatically applies a safety bevel on these small diameter lenses.
--Michael Urban, Gerber Coburn
Whenever I process children's eyewear on my own equipment, I have a hard time getting the tracing completed correctly. Why is this such a problem?
Solution
Children's eyewear does pose an edging challenge simply because it is so much smaller than adult eyewear. The PD is small and the tracing is sometimes difficult on today's patternless edgers because kids' eyewear doesn't fit in the tracer as well as larger frames. When you find yourself having trouble tracing, trace the frame's demo lens instead of the actual frame. Your measurements will be the same, and the demo lens will be easier to work with.
Some machines can alleviate this problem because they have B measurements that can go as low as 18mm. If you do a lot of children's eyewear, you'd be wise to invest in one of those machines.
Older equipment can also present more of a problem processing children's eyewear. Because the lenses are so small, the operators end up having to do more hand work, and that always presents possibilities for errors. Also, older technology sometimes is not able to produce a good, consistent bevel all the way around the lens.
The limitations of older equipment, especially when working with small or otherwise special jobs, is actually what prompts a lot of dispensers to update to the newer technology.
--Matt Vulich, AIT Industries
DON'T FORGET YOUR DUTY |
|
If you're dispensing eyewear to children, or any active patient, you need to be up to date on your Duty to Warn regarding lens safety. Duty to Warn became an issue for the optical community in recent years after the emergence of several lawsuits in which patients sustained injuries when their eyeglasses shattered during the course of physical activities. The maker of the lens and the lab that processed the lens are often named in the lawsuits. Furthering everyone's concern has been additional litigation in which the courts have consistently ruled that failure to warn patients about their options regarding lens materials justifies damage claims. This places a considerable burden on anyone dispensing eyewear to the public. Eyecare professionals are advised to always recommend polycarbonate or the new Trivex lens material, which is also impact-resistant, to children and even to adults who participate in active lifestyles. Once it is documented that they have been advised of the availability of such materials, your liability in the event of an injury is greatly reduced. The Optical Laboratories Association (OLA) has a guide to help eyecare professionals deal with this concern. The original Duty to Warn kit was recently revised with a number of items added to the package. It includes documents and scripts dispensers can follow when presenting impact-resistant lenses as an option. For information, contact the OLA at 800-477-5652 (www.ola-labs.org) or the Polycarbonate Lens Council at 800-944-6206 (www.polycarb.org) |
|
Problem
How can I avoid general lens surface damage when processing polycarbonate lenses?
Solution
Polycarbonate is lightweight and impact resistant, making it an excellent choice for children's eyewear. But it's a soft lens material, making it more vulnerable to surface damage during finishing.
With old style edgers, careful attention to chuck pressure helps to avoid problems, and some labs apply surfacing tape before edging to reduce scratches. With today's patternless edgers, edging polycarbonate is quick and easy because the machines electronically control lens clamping pressure to avoid problems.
Look for an edger that completes all processing steps automatically without lens removal, including rough cutting, beveling, safety beveling, grooving, and polishing. This minimizes handling and reduces the chances for damage
Wet edging systems should have an automatic continuous water spray system to keep the edging chamber clean and free of debris. And remember to keep the work area and job trays clean and free of surface particles that can cause spoilage.
--Tim Aiken, Briot-Weco USA