Testing
For Toughness
A Fresh Look at Safety and Lens Materials
By Joseph L. Bruneni
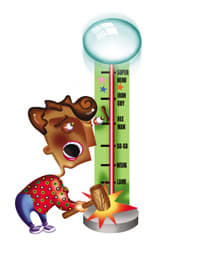
When it comes to eye protection, the United States is unique. This is the only country that mandates minimum impact protection for spectacle lenses. When all ophthalmic lenses were made of glass, there were numerous attempts to convince Congress to pass legislation requiring tempered lenses for consumer protection.
In the early 1970s, during a routine visit by optical industry leaders to the Food and Drug Administration (FDA), the FDA told the group that it could take years to get eyeglass safety legislated. Instead, they advised solving the problem with a simple FDA ruling.
As it turned out, such a ruling was issued very soon thereafter--in 1972--and from then until now, the U.S. has required that all ophthalmic lenses meet minimum impact resistance standards.
That ruling produced one unexpected result that would come to impact eyewear in the U.S. in a very significant way. It accelerated America's conversion from glass lenses to plastic. Even today, more than 30 years later, the U.S. is the only country that turned so completely away from glass. Though still popular in some categories, glass currently represents less than five percent of lens sales in the U.S.
COMFORT VERSUS SAFETY
Prior to the FDA ruling, glass lenses were often surfaced to 1.0mm center thickness, and it produced virtually no negative effect on optics. Following the new FDA regulation, however, glass lenses had to be no less than 2.2mm thick at their thinnest point.
The result was that consumers ordering new eyewear after the FDA decision quickly discovered that their new glasses were almost twice as heavy as what they had previously worn.
This produced an immediate acceleration of consumer interest in light-weight plastic lenses. What's especially interesting is that this U.S. conversion to plastic came about not because of safety concerns, but in order to satisfy public demand for lighter, more comfortable eyewear.
In the mid-1980s, the first lenses made of polycarbonate appeared in the marketplace. The total marketing emphasis on these new space-age lenses was on their superior strength, with the initial ads showing bullets bouncing off lenses made of polycarbonate. That early advertising did not, however, mention the fact that polycarbonate lenses were high index. In fact, it wasn't until the high index craze began in the early 1990s that poly was promoted for its high index benefits.
Even in the field of industrial eye safety--where it might be presumed that polycarbonate would become the standard--it did not take over the safety market. There appear to be two reasons for this. The first is cost and the fact that industrial safety contracts are often driven by price. This is understandable when a manufacturing company is responsible for providing safety glasses for thousands of people. Simply put, glass lenses are less costly than polycarbonate, and, thanks to economics, glass still plays a prominent role in industrial safety glasses.
The other factor is that, with one exception, the Z87 ANSI standard has never made a distinction between CR 39 and polycarbonate and acknowledged that poly at 2.0mm exceeds the impact resistance of CR 39 lenses at 3mm. As a result, industrial safety prescription lenses are still required to be 3.0mm at their thinnest point, whether made of CR 39 or polycarbonate. The one exception occurred when the standard was revised to permit plano poly lenses (used for the safety eyewear that visitors wear in industrial sites) to be only 2.0mm thick.
A revised Z87 standard has now been in the works for more than a year. It will permit not only poly, but also the new Trivex material prescription lenses, to be 2.0mm thick for industrial safety uses. Some Z87 members have protested this change, and, at presstime, 3.0mm prescription lenses are still required in poly for industrial safety eyewear.
THIN & LIGHT REVOLUTION
The growing interest in thin and light lenses in the early 1990s led to development of new high index plastic materials, and this brought the issue of safety back into the picture--especially for laboratories. Labs have always relied on lens manufacturers to advise them about safety issues concerning lenses and lens thickness. For years, manufacturers warranted that, when surfaced, their plastic lenses would pass FDA impact testing--the drop-ball test--as long as labs followed thickness charts published by each manufacturer.
When high index plastic lenses first became available--primarily from foreign manufacturers--the Optical Laboratories Association (OLA) was concerned that the impact resistance of some lenses, particularly when AR coated, did not meet FDA standards. The OLA invested substantial money to purchase and independently test those lenses. Some imported lenses failed, and some others were marginal.
Fortunately, this was early in the high index revolution, and when advised of OLA test results, changes were made in some high index resin formulas. Following those changes, lenses passed drop-ball testing, and concern over impact resistance of high index lenses faded.
The growing variety of lens materials, however, produced another change. For close to 30 years, lens manufacturers had, following FDA guidelines, performed statistical batch testing of their lenses and warranted that their plastic lenses, when processed properly, would meet or exceed FDA requirements. This changed a few years ago when, due to the growing variety of materials and the differing processes used in labs, manufacturers discontinued warranting plastic lenses. Since then, the lab has been responsible for impact resistance of surfaced plastic lenses.
Drop-ball testing a plastic lens can mar the surface and always risks damaging the lens. It's especially a problem with AR-coated lenses when as the steel ball strikes, it creates a small star fracture in the AR coating at the point of impact, large enough for the patient to notice. The lens has passed the drop-ball test, but it has been destroyed in the process.
For AR-coated stock lenses, this is not a problem. The manufacturer batch tests them. From every batch of 1,000 or so, they pull and test a certain number of lenses, discarding them after testing.
What constitutes failure? The FDA defines a lens has failed the drop-ball test when:
- The tested lens breaks into two or more pieces.
- Particulate matter is expelled from the backside of the lens.
Star fracturing of the AR coating does not constitute failure, so AR-coated stock lenses that do not break during batch testing meet the FDA requirement. If a representative number of lenses from a batch are tested without failing, the entire lot is said to meet FDA standards.
NEW SAFETY LENS MATERIAL |
|
Last year a tough new lens material called Trivex® became available from PPG, the company that developed and produced CR 39, used in conventional plastic lenses. Two lens manufacturers now produce lenses in Trivex. Younger Optics call its lenses Trilogy and Hoya calls its lenses Phoenix. Each company has modified the material to its own needs. What sets Trivex lenses apart from other plastics are:
The much-delayed revision to the Z87 standard for industrial eyewear mentions both polycarbonate and the new Trivex by name. The addition of this second impact-resistant lens material with favorable optical qualities should contribute to continued improvement in eye safety for eyewear consumers in this country. |
|
LAB'S RESPONSIBILITY
The OLA advised its members recently, that laboratories must now batch test their lens production daily. As a result, labs must determine how to test the vast variety of lenses that are processed every day in a typical facility. Lens materials, powers, designs, and thicknesses all vary, and in theory, each lens combination should be tested.
Though costly, statistical testing is the only way to deal with this wide range of variables. The OLA recently teamed up with Colts Laboratories, a Florida testing laboratory, to develop a laboratory certification program available only to OLA members. Following certification, the OLA lab must test--and then discard--two lenses per day. There are fairly substantial annual costs, but once a lab is certified, its daily testing costs can drop significantly.
What does all of this added emphasis on impact testing of lenses mean to eyecare professionals? Probably not very much. The FDA permits testing lenses in their uncut state, and this means there should be no increased FDA compliance problems for retail offices that edge lenses in-house.
It is important, however, to point out that compliance with the FDA requirement does not necessarily eliminate liability. For retail offices that do no edging, the confusing safety issues labs are currently dealing with simply means that doctors and dispensers can be reasonably confident that the eyewear they are dispensing to their patients is as safe as suppliers can make them.