Luxury is having your own personalized eyewear that stands out in a crowd. Fabricating fascinating eyewear is a rewarding challenge for ECPs
By Karlen McLean, ABOC, NCLC
PHOTOGRAPHY BY
PETER BAKER
MAKEUP BY
LESLIE STOEFFLER ATILES
HAIR STYLING BY
MILEXY
MODEL:
REBECCA LEIGH
West/Johnston Agency
fire Dazzling flames show the potential cutting-edge lens options for today's rimless eyewear by Matt Johnson
One-of-a-kind design is nothing new to the public or even to eyewear. Faceting was popular in the 1980s, and with today's equipment capabilities, customized lens shapes are easier than ever to achieve. With customers willing to invest in their own unique eyewear look, and becoming their own designers in some cases, ECPs are embracing customized lenses more than ever. It takes talent, daring, and business savvy to become successful in the custom eyewear market.
Here's how three ECPs have found their footing in a marketplace as unique as the lenses they create.
ICING ON THE CAKE
Customized lens treatment techniques are developed by experimentation, blending artistry and craftsmanship.
"We use a combination of hand files, diamond cutters, polishing wheels, diamond hand-stones, and nerves of steel," says Billy Brock, CO, of Billy Brock Eyewear Designs in Fort Worth, Texas. "We facet, sculpt, carve, do ledge cutting, and insert Swarovski crystals."
Two of the more typical customized lens types are gemstones and industrial.
The stones used most often are Swarovski crystals, however, diamonds and colored stones can be ordered and used as well. Diamonds come in four grades from promotional quality to VS (Very Small inclusion) quality. The stones are pre-set in brass, silver (.999), 14k gold, and 18k gold.
Another style choice seen in customization is less romantic and more industrial urban and streamlined. "Many clients are in love with a more industrial look," notes Matt Johnson, general manager of Eye-Q Optical with three locations in Boston. "A row of decorative screws or rivets can help provide that style."
HANDS ON
"The best way to ensure success is to take a plano lens and place it over your client's eye, trace the shape of the eyebrow and the eye itself, as well as any other lines you want to accentuate or ones you want to hide," advises Johnson.
This will make it easier to sketch out a shape that will flow with the client's features. Try to keep things in proportion; one line or angle left out or out of place can ruin the entire project.
Some of top lens customizing techniques include the following.
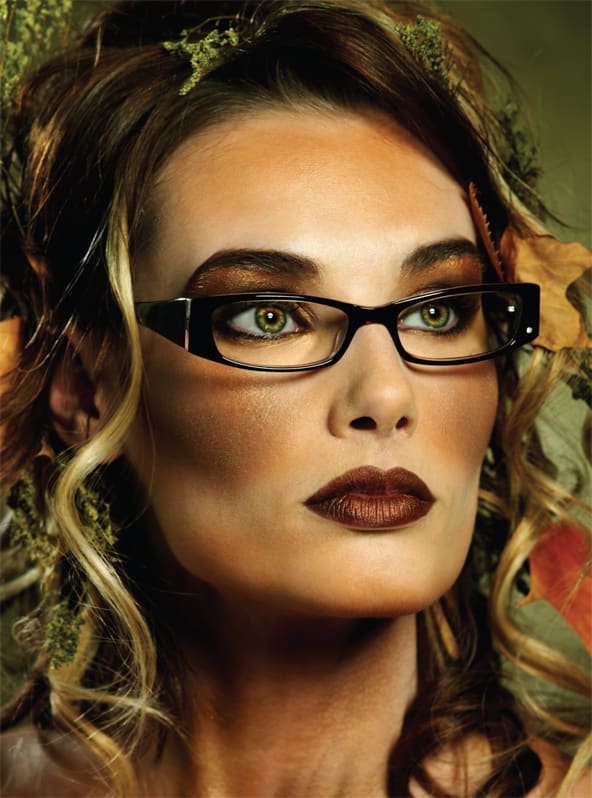
earth Initials and stones set in rimless sunwear highlight two custom techniques: airbrushing and stone setting by Harry Chilinguerian
experimental outreach |
---|
While everyone's a potential customized lens consumer, here are some specific samples of clients to cater to: Remember when. There was a time when many customized lens treatments were commonplace. Retired individuals get nostalgic when they see the very same options offered now—and they know the value of it. One and only. The patient who walks in and sees a bright color, unique shape, or one-of-a-kind style that they have to have. Contact lens wearers. CL wearers may have to stop using their contacts, which can make them unhappy. Special eyewear may help ease the transition. Money is no object. Some clients can spend anywhere from $500 to $900 on lenses alone at one practice. For them, diamond and other precious stones and materials are real options, if they are presented as such. Web users. Billy Brock's website www.billybrock.com has been in operation for about 10 years. Now, with a camera that shoots eyewear details in a way that's appealing to the public, the site is inspiring a wider scope of potential customized lens consumers. |
Airbrushing: Buy pre-cut stencils at beauty supply stores or nail shops. Use double-sided Scotch tape to hold stencils to the lens surface while air-brushing, utilizing fine particles of aluminum dioxide, commonly used for etching glass or metal.
To create custom-made stencils, take digital images and convert them to a usable format.
"I use GIMP (Gnu Image Manipulation Program) software, then print them onto transparency film," notes Harry Chilinguerian, ABOC-AC, NCLC, COA, of Dianne Bernitt and Associates dba Pearle Vision in Hunt Valley, Md. He then cuts the film with an exacto knife to create the stencil, which is approved by the patient prior to application.
Faceting: Using an 800 grit hand-stone with a six-inch radius, put a beveled edge on a lens to give it a sharp look. If using polycarbonate lenses, the wheel should be dry. For all other materials, use water to keep dust at a minimum. After beveling the edge with a hand-stone, use emery boards to smooth rough spots.
Then, polish the bevel to a high luster, masking any parts of the lens you want to protect from buffing wheel marks.
Lens overlay: Using custom spacers and long hex screws, a lens is cut as an accent piece, or a coinciding shape can be affixed to the front of the main lens. Measure precisely to ensure that the spacing is even between the lenses, and cut a test piece first to check alignment.
Racing grooves: This effect with horizontal lines can be achieved by running the front of the lens along the edge of the hand-stone. An 800 grit hand-stone with six-inch radius is best for the job, creating a texture that can be easily polished.
ground rules Profiting from custom lenses takes not only creativeness, but also business savvy. Some business guidelines include the following.
|
![]() water Setting stones in a variety of patterns appeals to many different demographic groups, notes designer Billy Brock |
Always use generous amounts of water for the best texture. A few layers of surface saver tape can be used as a guide as well to mask the lens to help prevent scratching.
"Horizontal lines make the piece look like it's going a hundred miles an hour even when it's just standing still," Johnson says.
Scroll cutting: This technique uses a series of drill bits and a stationary drill press to cut shapes that are too intricate for an edger.
Sanding requires the different textured bits and hours of polishing. A slow speed setting keeps heat to a minimum. Mask off as much of the lens as possible to prevent scratching.
Setting stones: Using a two-step drill bit places a hole within a hole with a diameter slightly smaller than the setting. The stones are held by the notch in the setting and the pressure from the lens. A handheld Dremel rotary tool is used on the lowest setting, 5,000 RPM.
Shape modification: Lens B measurements can be made larger to accommodate a PAL. To do this, mark the lens on the 180-degree meridian and scan it into the computer. From there, split the lens along the 180 mark and elongate. Often the slope of the nasal side of the lens also needs to be brought in to accommodate the elongation of the B size.
Print it out onto paper and measure to make sure the A size hasn't changed during the manipulation process. If it has, shrink the image by a ratio of original size/printed measured size.
Then, print the pattern onto heavy stock, trace it into the edger, and cut demo plano lenses for final patient approval and measurements. EB