eye on equipment
Processing Wrap Lenses
by Karlen McLean, ABOC, NCLC
Successfully fabricating high-wrap lenses in-office calls for a sports-based approach. Start with the right equipment. It helps prevent injury (to lenses) and improves eyewear performance. And it pays to keep the lines of communication open to stay up on the latest developments and knowledge.
"Communicating with your lab sales reps regarding the limitations for prescription wrap frames is essential," notes Matt Vulich, vice president, marketing for AIT Industries. "Even though the machines now can do a better job of this, it doesn't mean that all Rx's are open game."
Your game plan for high-performing high-wrap lenses starts here.
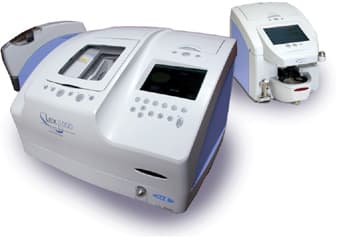
Fabricating wrap lenses in-house is easier than ever thanks to improved technology. Images: Santinelli Lex tracer and edger system (above) and Briot Alta NX-XL tracer and edger (below)
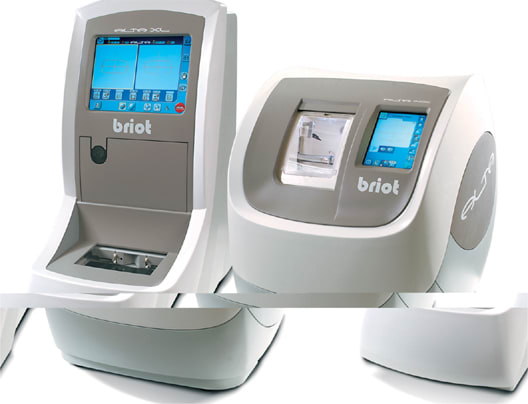
EDGERS
Invest in an edging system that's designed to do high-wrap lenses. Some key features to look for include:
1 3-D viewing screen. Advanced viewing screens allow operators to view the job before it's processed.
2 Adjustable processing. "It's helpful to have more than just one method of reproducing the most difficult frame shapes," notes Matt Menzies, sales and technical manager for Briot USA. "This may include imaging software that allows modification on all dimensions of the pattern to correct for any shape discrepancies from the original frame shape."
3 Customization capabilities. Being able to customize the lens bevel position, curvature, placement, bevel tilt, and bevel height plus being able to manipulate these areas to accommodate the eye wire profile is a premier function for processing wraps.
"It's key to be able to match the lens base curve to the frame base curve," says Franco Aluigi, product manager for Santinelli International. "If you're in a rush and using a stock lens, you can use a lens with a different base curve providing the equipment has the ability to manipulate the bevel position as closely as possible to the frame."
4 Advanced drilling capabilities. State-of-the-art edgers can drill high base curves up to 12mm, necessary to be able to accurately fabricate high-wrap, three-piece drill mounts.
5 Adjustable pressures and specialized roughing process. Adjustable pressures allow operators to safely and accurately edge various lens materials and coatings with less spoilage. Soft grind modes facilitate edging of super-AR lenses.
6 Advanced beveling and grooving capabilities. Precision groove and bevel placement ensures that lenses fit snugly in the frame.
Some edgers are designed with an option that allows a visual comparison of the bevel position as an on-screen graphic to help determine the actual bevel position before the lens is processed, so the operator can reposition the bevel and make adjustments without as much handwork.
Several edgers offer automatic internal and external safety bevels. For thin metal frames, an automatic mini-bevel function helps lenses fit accurately.
7 The Vision Council Data Communication Standard compliance. Sometimes referred to as an OMA standard, for ease of operation, all equipment should be compliant with The Vision Council Data Communication Standard, which defines the communication process between equipment and lab management software to keep things running smoothly.
QuickTips |
---|
The ability of a machine to create a variety of bevels, from 0.5mm to 3mm deep, is especially important with wrap frames. |
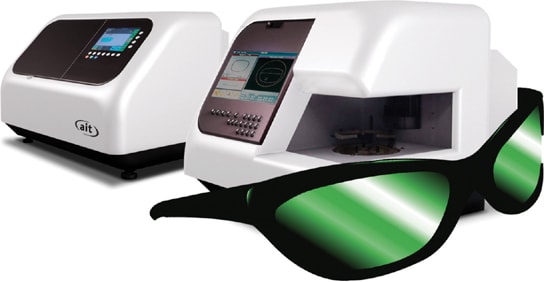
Above: AIT Industries Max tracer and edger; below: Gerber Coburn Rae tracer
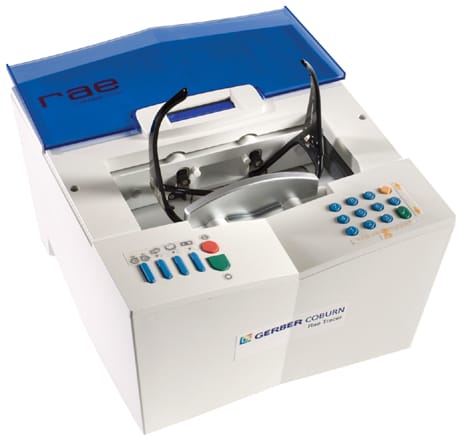
TRACERS
Tracing—getting the lens shape right—is a crucial area for processing wraps. Look for tracers with:
1 Multidimensional tracing capability. The ability to trace frames and demo lenses (especially rimless lenses) in multiple dimensions provides precise measurements, including A, B, frame curve, and elevation, essential in wrap lens fabrication success.
2 Large to small. Today's tracers accurately work with any size frame and makeup, including small children's sizes (18mm), large frames (70mm), extremely thin and/or flexible frames, and wrap frames. Tracing heads that incline help the tracer follow wrap frame chambers with very high curves.
3 Shape modification. User-friendly operation can include touch-screen displays that allow instant visualization of lens shape modification with wide angle rendering. Editing tools help create custom shape designs.
4 Easy loading and unloading. Auto-clamping and stylus insertion speeds cycle time. Simplified loading and unloading help avoid frame and shape distortion.
5 Data storage. Tracers are capable of storing many traces in internal memory. The amount of storage available varies from in the hundreds to thousands of traces. EB