troubleshooting tips
Caliper Conundrum
by Bill Harding
In my early days at Edward H. Schmidt and Sons, finer and polisher operators used hand calipers to check reference points around the lens to check for fining in unwanted prism. I always admired the step taken at that point in their lab to ensure quality. With today's technology this step is somewhat unnecessary other than troubleshooting and calibration.
However, thickness control is still of utmost importance. With digital thickness gauges, surface thickness control is quicker and more accurate—but the hand-held caliper serves the same function it always has.
And in our lab, we have them at several stations.
THICKNESS AND REJECTS
First inspection, mounting, and final inspection are the obvious stations, and we use hand calipers extensively in troubleshooting rejects. On minus power lenses, we always check center thickness with a reject for power, and with plus power lenses, it's usually easy to tell at the edger and assembly stations that an edge is too thick and we can do better.
We train our assembly people early on what thickness we need for different styles of mountings.
Most of the time, we find that thick lenses are related to block ring sizes at the surface blocker. Rarely is a thickness problem the result of a bad calculation from our lab management system.
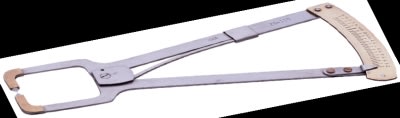
THEN AND NOW
Regarding thickness control in surfacing, today's modern technology contributes to a new level of calibration and maintenance that is much more precise than in the past.
Machines, especially generators, hold thickness and curve accuracy much closer and longer than the old diamond-wheel machines of the past.
● DIAMOND-WHEEL. In those days, wheel wear would contribute to a gradual change in thickness and curve. As operators spot-checked the lenses coming off the machine, they knew when a wheel change was creeping up on them.
● THREE-AXIS. Then the era of the three-axis generator came along. While cutter blade wear contributed to curve and thickness change, it was minute, and surface quality became more of a variable than thickness.
Checking thickness was not eliminated but a spot-checking of every few jobs was sufficient.
● ROBOTIC. We now have a robotic-loading digital generator, so, to avoid spoiling whole batches of lenses, we keep a closer eye on thickness with a digital gauge on the surface block. EB
Bill Harding is president, Lens Tech Optical Laboratory, Inc., in Greenwood, Ind.
QuickTips
We tell our assembly people not to pass on a pair of thick lenses that you wouldn't want your mom wearing!