Labs Give Input About Output
By Alex Yoho, ABOM
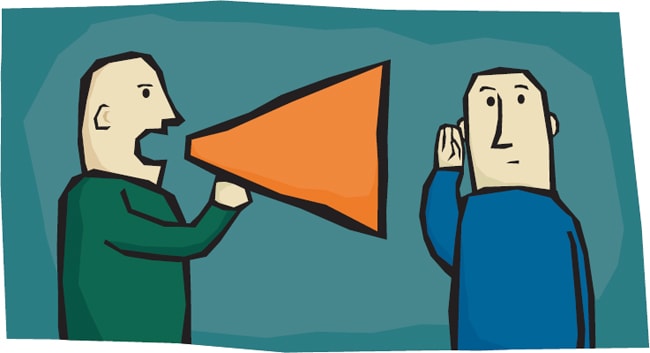
Sponsored by the Optical Lab Division of The Vision Council, this LAB Series article shows ECPs how to provide the best digital/free-form jobs.
Discussing both successes and challenges in this arena are the following member lab executives: Dale Parmenteri, vice president and partner, Balester Optical Company, Wilkes Barre, Pa.; Marc Wilson, ABOC and brand manager, digital surfacing, Essilor of America, Dallas, Texas; Jeff Szymanski, vice president, Toledo Optical Laboratory, Toledo, Ohio; Chris Bowers, operations, Walman Optical Co., Minneapolis; Barney Dougher, president, Hoya Vision Care, North America, Lewisville, Texas; Tom Brophy, director, Perfect Optics, Vista, Calif.; Jonathan Schwartz, executive vice president of operations, PFO Global, Irving, Texas; Bruce Calhoun, vice president, research and development, Riverside Opticalab Ltd., Ottawa, Ont., Canada; and Steve Sutherlin, president, Sutherlin Optical, Kansas City, Mo.
![]() |
Advice from member labs about digital and free-form best practices |
SUCCESSFUL FITTING
Q What can you suggest to ECPs for successful fittings?
PARMENTERI: One misconception is that digital is always thinner. Due to the fact that most digital designs are being done completely on the backside with single-vision blanks to start, thickness issues arise when a high plus exists with a high add. In these instances, we recommend using a dual-sided digital brand, resulting in a thinner lens.
WILSON: Digital surfacing does afford the opportunity for designs to incorporate additional patient measurements. These may be incorporated in the design, providing a personalized lens solution for each patient. Although several of these measurements may be taken manually (pantoscopic tilt, vertex distance, wrap angle), digital dispensing devices aid in collecting the most accurate measurements possible.
SZYMANSKI: It is the most misunderstood product in our industry. In order to be truly successful driving this category forward, an office must create the proper patient management process. This involves extracting needs, a proper doctor recommendation, and an effective hand-off.
BOWERS: Do not vary from the manufacturer’s instruction for fitting.
DOUGHER: Freeform lenses require optical staff to obtain additional information as compared with standard lenses. Collect all of the required information for ultimate patient personalization and satisfaction.
BROPHY: Don’t let variable designs become one-size-fits-all. Learn what each manufacturer offers in its entire product line, invest in the extra fitting equipment, and provide customized fitting information when possible.
SCHWARTZ: Success in dispensing progressives is dependent on accurate fitting and manufacturing to the ordered specifications. It always has been, and always will be. New technology is becoming available…that will measure insets accurately as the lens designs will move in the direction of variable insets based on individual patient needs.
CALHOUN: Fitting accuracy is crucial, and using suitably sized frames with a minimum B dimension that enables at least 10mm above minimum fitting height is important.
SUTHERLIN: For entry-level digital designs there are literally no extra steps required. However, we have the ability to take the optics to a much higher level now, but it does require a commitment from the eyecare practitioner to take far more sophisticated measurements. Attempting to take these measurements manually is an invitation to disaster.
ENHANCING THE EXPERIENCE | |
---|---|
![]() |
Here are a few tips from the experts about building patient satisfaction. CALHOUN: We encourage dispensers…to get patient feedback. A few ‘WOW’ experiences will build that confidence in a hurry. DOUGHER: Scripting at the practice level is very important. Generally, it boils down to knowing your patients and being a good listener. SZYMANSKI: A discussion with the patient about realistic expectations will [help] ensure success. |
PROBLEMS/SOLUTIONS
Q What are the contributing factors when a job fails?
PARMENTERI: Some dispensers have difficulty adjusting to the engravings. The prescription, base curve, scratch coating, and lens vendor can affect the engravings, sometimes being considered too light or too intense by the dispenser, creating a spoilage category for the lab. The dispenser must trust in the digital calculations made at the lab. Bumping up the add or messing with the seg height does not work with digitally designed lenses.
WILSON: Process control within a laboratory becomes much more important. With a traditionally surfaced PAL, the design is faithfully maintained on the front side. The lab only surfaces the distance Rx on the back. However, with a digitally surfaced FBS (full back surface) lens, the lab is surfacing both the distance Rx and the actual progressive design on the backside. If the lab’s equipment or processing parameters are not optimized or calibrated, the integrity of that intended design may not be faithfully maintained.
SZYMANSKI: We have seen a negligible failure rate in large part because we have taken the time to educate folks about performance and the process we need to take in order to ensure a sensational outcome.
BOWERS: There is very little failure. The ones we do see are usually digital wrap that exceeds recommendations for size and power.
DOUGHER: You don’t want to start blaming people for not understanding a new technology like free-form lenses. The math behind how they work is very complicated, so everyone needs to help each other climb the learning curve. Our quality control system will not release a job without a quality card, which is essentially a tag that tells us the lenses produced meet the prescription provided.
BROPHY: If no customized data is given, the free-form file is calculated with default values for wrap and vertex. This can create a compensated value, which some patients have a hard time with.
SCHWARTZ: The most common error is being fit too low. Most designs are manufactured to allow the fitting cross to be placed at the true optical axes when the patient is in their normal posture, which is some degree of inclination.
CALHOUN: Our experience has been that 99 percent of non-adapts are due to dispensers not understanding or following fitting parameters—such as minimum fitting heights not being respected, incorrect frame adjustment… or frame selection resulting in loss of near area as the add is edged away. Due to the CNC operation, machine or human errors are minimized to the extreme, and quality control is able to filter that type of defective lens out.
SUTHERLIN: When an Rx fails, it’s quite often because the patient has not been educated as to what their expectations should be. To completely fulfill the patient’s visual needs in all circumstances, we recommend three pairs—an excellent all-purpose design, a computer/room distance design, and a pair of polarized.
DEFINING TERMS | |
---|---|
![]() |
“Digital” refers to surfacing methods that translate a lens design from computer software to computer numeric control (CNC) machinery which can put any shape on a lens surface. It’s somewhat of a catch-all term used for anything from enhancing existing lens designs like progressives to creating the entire design on the back surface—distance Rx, progressive, and all—utilizing this CNC “free-form” across the lens surface. |
POSITIONING POINTERS
Q Some dispensers are reluctant to recommend digital/freeform lenses due to price. How can they overcome this?
PARMENTERI: The technology has given the doctor the ultimate ability to design a lens for each patient. Now labs are private labeling, creating digital designs that are conventionally priced, removing the price barrier.
WILSON: Just because a lens is digitally surfaced does not necessarily justify a premium price. What digital surfacing DOES is afford the opportunity to personalize the design to each patient’s needs.
SZYMANSKI: [Our] industry is notorious for pre-judging and not making recommendations for fear patients/customers might balk. The slight price increase is completely justified when you consider (and properly explain) that we’re also providing an unmatched degree of precision and customization.
DOUGHER: Within our “good, better, best” options, it is possible for all our lenses to be free-form. So…an ECP can get any patient into a free-form lens at almost any price point.
BROPHY: Many digital progressives are now less expensive than conventional lenses. Labs are making the pricing more attractive so they don't have to keep such a large inventory.
SCHWARTZ: Let the patient decide if he wants the highest form of visual performance available and present the lenses with all the true benefits.
CALHOUN: [Stress] the benefits of free-form technology: crystal-clear, extremely wide viewing areas; expanded peripheral with minimal distortion; greatly reduced swim; and the widest choice of materials.
SUTHERLIN: The best comparison is television. We thought we were seeing great pictures 10 years ago, but who would want to give up their high-definition set today?
THE FUTURE
Q What does the future hold for digitally enhanced, free-form lenses?
CALHOUN: We will see the actual refraction interface with the lens design to achieve personalized lenses.
BROPHY: A day when a stock room with only single vision lenses may be all that’s required.
SZYMANSKI: What’s ahead? Freeform and digitally fabricated lenses will be the future! EB