Transforming Design to Reality
What you need to know to understand and communicate the “digital” process
By Alex Yoho, ABOM
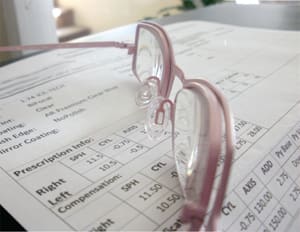
Photo courtesy of ICE-TECH Advanced Lens Technologies
Those of us who have grown up in our business have seen some truly amazing advances in lens design and the effects of positioning a lens before the eye. An historic paradigm shift has been occurring right before our eyes with this technology we so loosely call “digital lenses.”
There seems to be a lack of understanding as to just what the term “digital” means, how it’s used among ECPs, and how the process is communicated to the consumer. This article, sponsored by The Optical Lab Division of The Vision Council, will give you the tools to develop your own way of describing “digital” to patients and customers.
DESIGN ASPECT
First, let’s go back to the design aspect of this process. Scientists have long understood many things about how light refracts through a lens. There’s the basic bending of light rays known as first order optics, which is central to what is used on a daily basis to correct nearsightedness, farsightedness, astigmatism, and prism.
This article is sponsored by the Optical Lab Division of The Vision Council
TAKING MEASUREMENTS |
---|
VSPOne Optical Technology Centers production managers Chris Ballani and Rodney Betz say that although adaptation issues are very rare with digitally surfaced designs, “when we hear of issues, we usually find that the patient’s measurements were either not provided or not accurately measured. With today’s advanced digital designs, PD sticks and guessing at wrap angles won’t produce good results. These new, highly precise lens designs require equally precise measurements—such as pantoscopic tilt, vertex distance, OC height, and frame wrap—in order for the patient to experience the full potential of the lens design. There are many options available across the industry to obtain the needed measurements.” |
As understanding of refraction increased, lens designers learned they could control some distortions and aberrations that occur with eyeglass lenses. Some distortions were corrected by defining and addressing things like base curves and using aspheric surfaces, but other aberrations remain.
Though digital surfacing makes it possible to control the lens surface, this highly accurate technology can be used to grind some of the most exotic progressive lenses imaginable. It can be used just as easily to grind a regular plain-vanilla single vision lens.
In other words, “digital” does not always mean better. What makes the difference is the translation of optical science theories that reduce higher-order aberrations by considering wearing position, material, and size of frame to the lens designs.
THE LAB PERSPECTIVE
A discussion about “digital” with a number of lab executives brought many critical factors to light.
According to Chris Bowers, operations manager with Walman Optical, “The whole digital realm as it relates to quality and service is a carefully choreographed concert between the lab, lens design software (LDS), and the laboratory management system (LMS).
“The designs are theoretical,” he adds. “The manufacturing is mostly accomplished at the lab, but under ‘best practices and procedures’ enforced by the designers. Quality control sampling is a part of the process that compares the design to the lenses that are being ground.”
QUALITY CONTROL SHIFT |
---|
Lens image courtesy of Younger Optics ![]() Rick Tinson, vice president of inventory and distribution for HOYA Vision Care, emphasizes that with free-form, “the essential quality control step has moved from the factory to the laboratory, requiring a whole new level of quality assurance beyond just checking powers in a lensometer.” This fundamental shift is a big topic. VSPOne Optical Technology Centers’ Ballani and Betz agree that with digital lenses, laboratories are now responsible for creating the entire power progression in the lens. This is critical for ECPs to understand when considering what lab to use. |
SELECTING A LAB |
---|
ECPs should make the quality of design replication—getting the precise lens design they ordered—a top criterion when choosing a lab partner. This starts with having a frank, in-depth discussion about the quality-assurance processes in place for any labs they are considering. Also, if at all possible, scheduling a trip to tour the lab and seeing it firsthand should be part of the selection process. It can be an invaluable validation and educational step for anyone in the office responsible for communicating the importance of quality with customers. |
Chris Ballani and Rodney Betz, production managers with VSPOne Optical Technology Centers, explain how digital surfacing differs mechanically from traditional surfacing: “To achieve the desired power, traditional surfacing uses fixed-curve lap tools and fining pads matched to cut the back curve. This technology is limited to an accuracy of either 1/8 or 1/10 diopter, depending on the tool set the lab has chosen as its basis.”
Digital surfacing, on the other hand, does not have these limitations as it uses a small, natural diamond-cutting tool, sophisticated software, and equipment enabling a complex curve to be cut on the back surface of the lens. This allows generation of power accuracy to the hundredth of a diopter, explain Ballani and Betz, and an almost unlimited breadth of design options for customized prescriptions.
NEW METHODS
Ensuring quality control at the lab requires methods that were never used before. New instrumentation has been developed and several processes are used to determine the lens prescription and to verify that it matches the designers’ intended parameters. Adam Winkelman, brand manager, West, for VSP. explains that “all digital lenses we produce have the power checked to a .01 diopter.”
Bowers adds that daily samples are sent to the lens design software (LDS) vendor for validations. Betz and Ballani mention there is now both equipment and mapping processes that validate power accuracy over the entire surface of the lens at 1,500 inspection points.
TALKING TO PATIENTS
How do you explain all this to patients and stress why they should buy digitally surfaced designs? “They need to know that the lenses have been made uniquely for them,” Bowers says. Ballani and Betz add: “From a consumer perspective, the digital lens difference is really about getting the most precise prescription possible. We often give [patients] an analogy of comparing a suit off the rack to a suit you have tailored to fit—they both work, but the tailored one is a lot better.”
There is no one-size-fits-all, however, stresses Bowers. “The dispenser needs to evaluate the patient’s lifestyle needs and may even recommend more than one pair of glasses.” Adds Winkelman, “Ask lifestyle questions. This ensures [the ECP] dispenses a lens design and uses the proper fitting heights as it relates to that patient’s needs.”
Richard Hughes, president and MIS manager at Beitler McKee Optical Company, says he worries about misinformation. “I hear a lot of ECPs claim that they sell the ‘best lenses in the market’ and when asked what that is, their answer is ’digital.’ That’s a shame for all the lens manufacturers that work hard on delivering real technology design offerings to the market place.”
Drake McLean, president of Dietz-McLean, sums it up: “If you consider that we are selling the most advanced lenses, with advanced treatments at advanced prices, we better have an excellent story with understandable data and facts to back it up.” EB