eye on equipment
Beveling For a Better Marriage
Susan Tarrant
The bevel—that (usually) V-shaped cut on the lens edge that allows the lens to sit securely in the frame—was once the domain of lens techs with hand tools.
These days, it is cut in seconds as one of many automated steps in the contemporary edging process.
Though the advances in lens finishing technology have made beveling a relative snap, the advances in lens materials, lens surfacing techniques, and frame curvatures have made the importance of placing just the right bevel in the just the right spot more important than ever.
Luckily for in-office labs, contemporary edgers are well-versed in bevel design, with most models offering a host of bevels and locations, and allowing the operator to customize the bevel to the frame at hand. This advancement has allowed for labs to achieve, as one field tech calls it, “the perfect marriage of frame and lens.”
We asked some experts in the field from Santinelli International, Briot USA, and Coburn Technologies to weigh in on what customized beveling has meant for in-office lab performance and patient satisfaction, and how it has made it possible for more jobs to stay in-house.
THE CHALLENGES
The goal of modern edging is to let the edger do the work that used to be finished, or at least finessed, by hand. Modern edgers are able to perform adjustments to the lens bevel to match the curve or the frame. No small feat considering the range of prescriptions and lens materials and the variety of frame curves.
After tracing, the edger can tell exactly what the frame curve is. As it maps the lens, it can calculate the average bevel curve. One number (frame curve) is fixed, and the other can be adjusted in order to best fit the curve.
That gets trickier when you get two parts of the whole that don’t naturally make for a perfect fit. It is a process that has some inherent challenges.
■ HIGH-MINUS LENSES IN HIGH-WRAP FRAMES. Fitting the average bevel curve into a higher-wrap frame often causes the temples to splay.
■ HIGH-PLUS LENSES IN FLATTER FRAMES. The average bevel curve might be higher than the curve number, causing the lens to pop out a bit at the top.
■ VISUALIZATION. When choosing a bevel position, it can be hard to visualize the actual position of the bevel along with the specifics on the lens thickness.
■ COMPROMISE. Compromising optic value for the cosmetics of the frame/lens fit results in non-adapts or unhappy patients.
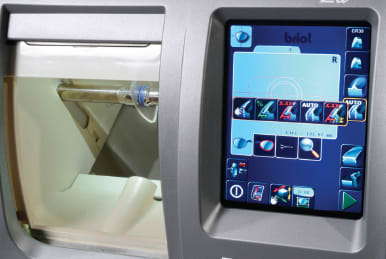
Image courtesy of Briot USA
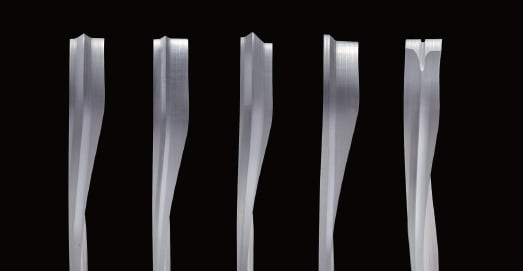
Image courtesy of Coburn Technologies
Furthermore, many of today’s frame materials, such as stainless steel or unforgiving zyl, are too rigid for frame flexing to accommodate for the variance between the frame and bevel curves. And it’s just as well, too. Customizing bevels have all but done away with the need for hand twisting and bending.
MAKING MATCHES
There are many ways to achieve the perfect marriage of lens and frame, and most edger models today provide plenty of choices to make it work.
Choices of height and dimensions include standard bevel (equal dimensions front/back) or mini-bevel (the height can be reduced to minimize the exposed surface beyond the eyewire of the frame).
To get even fancier, you can choose various angles, tilts, and shapes, including a shelf (or step) bevel that tapers in the exposed back edge of lens. The latter is particularly useful in high wraps.
How easy is it? Fairly. Calculations are done automatically. In most cases, ideal bevels are suggested.
Though the display mode will differ from model to model, some can even display a graphic representation of the bevel choices before a decision is ultimately made. The same menu provides adjustments via on-screen controls and uses multiple viewing angles for reference.
With an advanced edger, there should no longer be a need to “tweak” or otherwise compromise a frame with pliers to reach that perfect fit. And, with so many customized bevels at your automatic disposal, there is no longer a need to compromise optic value for cosmetic appeal.
YOU Can Do It
Would you like to have a better handle on the lenses that come out of your in-office edger?
The latest lens finishing technology allows operators to choose the bevel placement that’s best for the lens and frame style at hand. And the best way to ensure that you are using the edger (and its bevel options) to its fullest potential? Call your equipment manufacturer representative and ask for additional training.
“An edger is only as useful as you are motivated to learn it well and are supported by a company that shows you how to run it to its fullest potential through real worldstyle training in the field,” says Jaysun Barr, ABOC, territory sales manager for Santinelli International.
In other words… you paid for it, so make sure somebody trains you how to unlock ALL the bells the whistles.
PATIENT SERVICE
Being able to customize bevel design and placement is a huge advancement in in-house equipment. And it’s one that can have a huge affect on patient service.
It now allows ECPs the ability to service a wider range of frame styles in-house than ever before—including high-wrap sunwear. And, as the technology advances even further, it is opening up a wider range of prescriptions (including high minus and plus) to a wider range of frame styles.
In addition, like everything about in-house finishing, it’s a great way for ECPs to differentiate their service from those practices that send everything to the lab. In fact, some of the easiest ways to differentiate your practice from your competition is to focus on the elements of service that matter most to patients—proper fit and optimum optics.
Creating the perfect match of frame and lens fit will also make for a couple of other perfect matches: eyeglasses and wearer, and patient and practice. EB