retail ops
Resistance vs.Proof
Karlen McLean
Communicating the difference between two commonly used terms— proof and resistant—can impact several things. First, whether a sale is made and, later, if lenses are scratched or frames broken, whether clients are dissatisfied or satisfied.
The best approach, say most ECPs, is one that’s upfront and direct. “When I discuss lenses with a patient, I state that no lens, no matter what material, is scratch-proof or breakage-free,” says Bev Heishman, optician at West Reading Optical in West Reading, PA.
She tells clients: “Scratch-resistant treatments are designed to make lenses more durable for everyday circumstances; they are not scratch proof. With proper care in everyday circumstances, they’ll hold up.”
TALKING SCRATCHES
Doctor involvement can help consumers understand lens capabilities and instill reasonable expectations. For example, Henry Oishi, OD, of Eye Appeal Optometry in Temecula, CA, explains: “‘Mr. Smith, the lenses you’ll be getting for your safety eyewear are scratch-resistant, but they are not scratch-proof. This means you can still get a rock and scratch the lenses.’ I also mention that [our] scratch-resistant lenses come with a one-year warranty.”
Explaining warranties also helps clients be realistic about eyewear performance. “Mention warranties and what it takes to exercise the warranty, ensuring that you [explain that] anything can scratch given the right opportunity,” advises consultant Diane F. Drake, LDO, ABOM, of Jackson, GA. “The ECP’s role is to fully educate on impact resistance without using the words ‘shatterproof’ or ‘unbreakable.’”
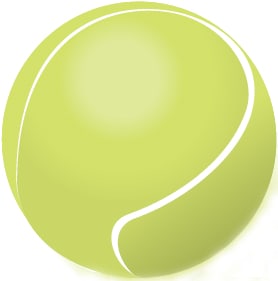
TRUE SAFETY
Selling ANSI-approved safety eyewear elevates scratch and breakage issues to topics like health, safety, and welfare.
“If you educate clients on the visual differences of a safety lens versus a dress polycarbonate lens, for example, it’s usually easier for them to grasp,” explains Melinda M. Jester, LDO, president and CEO of W2 Technologies, Inc., a safety eyewear company based in Orlando, FL. “An ANSI [approved] lens is always monogrammed on the temporal corners of the lens with a mark indicating the lab that generated and tested the lens. If this is absent, it’s not a real safety lens.”
HOW SAFE IS SAFE? |
---|
“If a safety lens lessens an impact or prevents an injury, it’s done its job,” points out Airgas/Protective Optics’ Jim Knapp. “Nothing is unbreakable. Safety glasses are tested to withstand a certain impact of a certain size projectile. According to ANSI standards: ‘Lenses shall be capable of resisting impact from a 6.35mm (1/4 inch) steel ball traveling at 45.7m/s (150ft/s).’” |
“To help determine recommendations, the first thing I do is ask the patient to explain what he does at work—his possible impact potential and exposure to abrasives, chemicals, splatter, or debris,” says Jim Knapp, Protective Optics customer service lead for Airgas/Protective Optics in Germantown, WI. “I use the analogy that anything is breakable, it just depends on what it’s hit with. A BB may bounce off the lens, but an anvil will crush it. Size and velocity matter.”
It’s important to correct misconceptions, warns Knapp. “Most of my customers hear ‘safety glasses’ and immediately think ‘unbreakable.’ As ECPs, we must educate them to the reality of safety glasses without damaging [their] credibility.” EB