lens tips
Who’s Afraid of Rimless?
Erinn Morgan
Rimless isn’t what it used to be. In fact, high-tech frame and lens materials have made rimless eyewear more durable and easier to process than ever before.
“We have a Smart Drill here and we do our own drilling in-house,” says Bill Curran, owner of William Curran & Son in Drexel Hill, PA. “We don’t trust anyone else, and because we’re designing our own shapes, we need to be doing it in-house anyway.”
Lonnie Burrow, owner of the ultra-high-end Burrow Optical in Little Rock, AK, agrees, as all of his rimless processing is done in-house.
“We do all our rimless work right here except for Italee 2.5, which is processed in their own lab in California,” he says. “We can’t send a $2,000 frame to a lab somewhere where we don’t know who will be handling it and bending it and possibly losing precious stones.”
Still, some eyecare professionals remain wary of selling and processing rimless drill mounts.
“When I first started in this business in 1970, rimless glasses were made with glass lenses,” says Sandy Lesnick, owner of Lesnick Optical, Belleville Vision Center, and VisionPro Eyecare in the Detroit metro area. “When they drilled a hole through them they were very susceptible to breakage, and this held rimless back from being more popular at the time.”
Instead of rimless, Lesnick began recommending nylon rimless (i.e., semi-rimless) frame styles as an option to customers.
But times have brought about dramatic change. And while lens manufacturers have delivered stronger, lighter lenses well-suited to rimless processing, labs have also learned how to better work with this unique frame category.
Rimless lens materials of choice are polycarbonate and Trivex. But PPG is introducing the Tribrid lens, which is a Trivex/high-index hybrid material suitable for rimless eyewear.
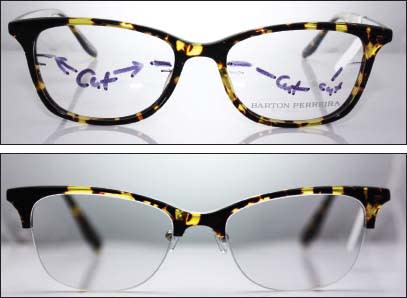
LUXE Laboratory crafted a rimless request with a Barton Perreira frame by cutting the plastic off of the bottom and making it semi-rimless, then adding titanium nosepads
PERMANENT CHANGES
Eyecare Business recently checked in with rimless processing expert Richard Wilhelm, owner of the high-end LUXE Laboratory in Anaheim, CA, and his veteran team (including customer service manager David Golub and lab manager Pete Gonzales), on how crafting complete rimless Rx eyewear has changed for the better.
1 What is the difficulty level of processing rimless eyewear in the lab today?
In my 14 years of processing traditional drill-mount rimless prescriptions, it has never been easier. At LUXE, at least 80 percent of our work is rimless. We have all the new equipment needed. Still, rimless eyewear will most likely always remain the most challenging—and fulfilling—of all.
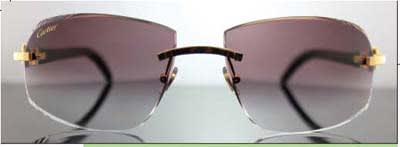
2 Why is rimless processing a fulfilling endeavor?
Our roots are deeply embedded in rimless eyewear. Our rimless work provides a constant change rather than the monotonous work of simply snapping in lenses.
It keeps things fresh in the lab. It provides a sense of gratification when a true work of craftsmanship is completed all in the name of helping people see.
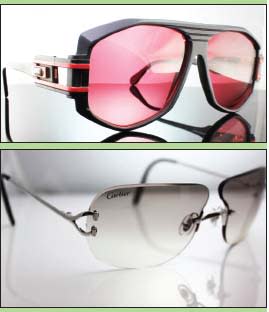
LUXE Laboratory’s high-end processing includes jobs such as (from top) unique faceting on a Cartier rimless frame, a custom tint on a Cazal frame, a Cartier rimless frame with a difficult custom lens shape, as well as a luxury project with a perfectly round Mykita frame with horn inset and 18kt gold plating. All images courtesy of LUXE Laboratory
3 What’s made processing rimless easier today?
Technology over the past decade has helped in all areas of the lab. High-tech edgers, once only exclusive to mega labs and corporate labs, are now affordable for the independent ones. The lab industry has actually had to keep up with the frame industry as new frame lines are released with special bevels and venting systems—rimless eyewear has not been excluded from the need for multi-axis edgers. Shapes are now common on high-wrap rimless pieces where a three-axis edger is just not sufficient any longer.
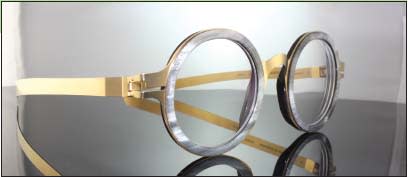
4 What’s your favorite lens material for rimless?
New lens designs have made processing rimless easier. Trivex or 1.67 are the main materials we use. We really love Trivex. About 75 percent of our rimless work at LUXE calls for high base curves. The newer wrap lens designs such as the [Shamir] Autograph Attitude have allowed us to provide an optically sound lens.
5 How difficult—or easy—is it for ECPs to work with groove mounts?
You do really need to bring groove mounts into the picture when talking about rimless. The two are completely different animals, but there are more possibilities for mistakes on a semi-rimless groove mount than a drill hole only. EB