HOW I...
Working Smarter, Not Harder
How one Florida optical lab increased its capacity after a thorough analysis
rolando Domingo used to describe his optical lab’s production line as “a chaotic mess.” The lab, Best Price Digital Lenses in Pensacola, FL, was plagued by the same good problem that many labs have: an increase in work. But the lab’s production process wasn’t keeping up well.
“Our lens demand was growing. We were receiving shipments of over 100 lenses a day and were spending almost half the day just sorting through the lenses and placing them in the correct bins,” he recalls. “Our lab process just wasn’t working for us anymore.”
THE CHALLENGE
Knowing a change was needed, Domingo decided to have an analysis done of his production process to find efficiencies that would allow his staff and equipment to work smarter and better, not harder and more chaotic. He enlisted Practice CoPilot, a company specializing in “lean” practice management and cutting-edge technology. The goal of the analysis was to understand and increase capacity while eliminating waste.
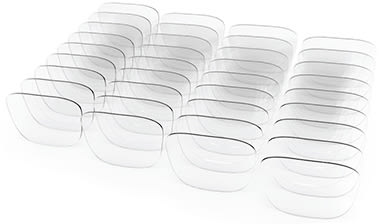
THE PROCESS
The entire lab process was filmed, station by station, so time studies could be conducted on machines and operators to determine the ideal layout for maximum production.
“We identified the constraining steps in the lab process and built around them for optimization of production without additional expenses such as space, staff, and equipment,” explains Tony Milian, co-owner of Practice CoPilot.
The positioning of the production was also analyzed and, in some cases, reconfigured, so that the resources were placed where the work was to be performed, not just where there was space. It minimized a lot of wasted movements for staff and allowed for an increase of productivity.
PROBLEMS AND SOLUTIONS
Like many labs similar to them, Best Price Digital Lenses faced the biggest problems in its shipping and receiving processes.
PROBLEM: The lab was receiving over 100 lenses a day that needed to be sorted and placed in proper trays. Hours were spent in the sorting stage instead of the production stage.
PROBLEM: At the shipping stage, staff would have to stop production at 3 p.m. every day in order to fill the orders to be ready for shipment.
It was an unorganized flow of product and manpower.
SOLUTION: By refining the production line, shipping was implemented into the final inspection where, going forward, lenses would be packaged and ready to ship.
The shipping station was entirely eliminated, and with the newly executed plan, 150 orders were filled every day instead of only 70, and with three fewer full-time employees. The whole process became continuous, like a wheel.
“We became a well-oiled machine,” reports Domingo. “It wasn’t about better ideas, it was all about the layout and engineering the actual lab process. I’ve been doing this for 20 years and kept thinking there wasn’t anything I haven’t thought of already, but it wasn’t about that.”