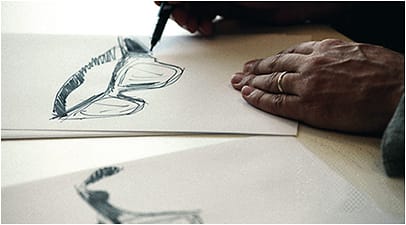
Who is Safilo? The world’s second-largest eyewear creator, manufacturer and worldwide distributor of sunglasses, optical frames, and sports eyewear, Safilo Group has an iconic legacy dating back to 1878.
In fact, the company’s optical origins began when the oldest Italian industrial complex for producing lenses and frames was established in Italy’s Cadore area in 1878. Today, Safilo boasts seven owned, high-volume production plants plus innovation-driven design studios in Milan, Padua, New York, Hong Kong, and Portland, OR.
The company also lays claim to an impressive and exciting portfolio of eyewear brands, including five proprietary brands and 25 licensed brands. Safilo’s brands fall within five enticing categories—Atelier (Elie Saab + OXYDO), Fashion Luxury (from Dior and FENDI to Jimmy Choo), Contemporary Fashion & Lifestyle (from Kate Spade and Tommy Hilfiger to Carrera), Mass/Cool (from Havaianas to Polaroid), and Sport & Outdoor (Smith).
Safilo’s Core Principles:
» Integrity
» Respect
» Accountability
» Simplicity
» Interdependence
» Sustainability
A Global Leader
An extraordinary lineup of production facilities enables Safilo to experiment with design, non- traditional materials and shapes, creating products and setting leading worldwide trends. Here, a listing of Safilo’s seven manufacturing sites, including each factory’s specialty area of focus:
Production Site | Specialty |
---|---|
Longarone, Italy | Metalworking + Stainless Steel Production |
Martignacco, Italy | Injected Eyewear + Acetate Production |
Santa Maria di Sala, Italy | Acetate Production |
Lenti, Italy | Graphic-Design Sunlenses |
Ormoz, Slovenia | Optyl Production |
Clearfield, Utah | Smith Goggles Production |
Suzhou, RPC | The First Facility to Support End-to-End Production for All Technologies |
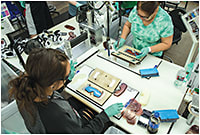
Safilo: A Manufacturing Reinvention
What is the future of Safilo? The company’s 2020 Strategic Plan aims to take internal eyewear production from 30% in 2015 to 70% by 2020. This revolutionary goal aims to design an agile, synchronized, yet differentiated end-to-end supply network with superior responsiveness and quality. The path to success? A manufacturing network reinvention through a $60 million euro investment in infrastructure. Safilo’s facilities are currently being modernized to reach an even higher level of ability to serve the market, including enhancements in production lead time, product quality, inventory, and cost management.
Tremendous investments in human resources and technology (new equipment boasting cutting-edge tech) are the starting point of this vast transformation plan. Manufacturing flows and plant layouts are also being redesigned.
The ultimate goal—a manufacturing system that is fully able to manage the entire cycle of production end-to-end for each pair of glasses. This strategic innovation has already debuted at Safilo’s plant in Suzhou, China, which has revealed an overall production lead time reduction of 40%. Remarkably, finished frame lead time has dropped from 35 days to 22 days.
A strategic advantage—an organization that is capable of responding quickly and appropriately to current market needs. The future is so very bright at Safilo.
Did You Know?
Safilo has a dedicated area of its factory in Longarone for stainless steel production—the best quality standards are guaranteed by highly skilled workers and sophisticated control procedures.
An Insider Look
By Erinn Morgan, Editor-in-Chief, Eyecare Business
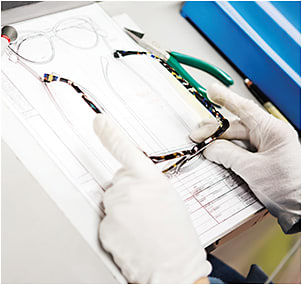
The energy was palpable. Everyone had a purpose, the high-tech machines were humming, hundreds of highly skilled craftspeople were doing hand work, and ultimate-quality, beautifully designed, and expertly produced eyewear was the focus.
I was near Padua, Italy, with the privilege to experience a tremendous eyewear manufacturing facility in person—Safilo’s state-of-the-art Santa Maria di Sala eyewear factory. The mission here—to produce the very best high-end acetate eyewear in the market.
Up close and in person, the factory was even more impressive than I’d imagined. A full 17,000 square meters of production space, the facility employs around 800 people, and has the capacity to produce 2 million pairs of eyewear each year.
The plant, founded in 1964, is the oldest Safilo site currently operating, yet it is clearly modern and high-tech in its nature. New, cutting-edge production equipment—part of Safilo’s behemoth investment into its manufacturing reinvention—is everywhere. Hundreds of highly skilled craftspeople assemble everything, from temple and frame fronts to hinges, logos, and crystals, all expertly, all by hand. The amount of hand work still done today by Safilo’s facilities is truly impressive. A feature that makes this market leader notably special.
Art, Beyond the Frame
Extraordinary graphics. Modern 3D looks. Stunning mirror effects.
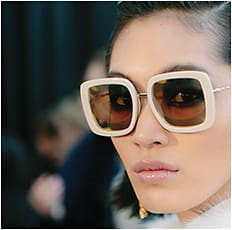
Highly unique, aesthetic lenses are becoming a new focal point for eyewear, and Safilo is leading the way. With the recent acquisition of Lenti, the sun lens manufacturer based in Bergamo, Italy, Safilo now lays claim to an increased capacity and improved time to market for sunwear production. It also boasts some of the most state-of-the-art manufacturing capabilities and processes for “Made in Italy” lenses.
Safilo’s groundbreaking decorative lens designs include 3D looks with prismatic or tactile effects, bi-color shaded lenses exclusive to certain collections, high-vacuum mirrored lens treatments with exclusive color combos, and iridescent effects achieved by a multi-layer coating process.
The result? Head-turning eyewear from all angles.
Hand Built in the USA
Beep! Beep! Beep! The worker-operated loading carts whiz by. This factory has its own energy—fast, highly efficient, and yet, just like its brand’s tenets, fun-loving. I am at the Smith eyewear factory in Clearfield, UT, just outside of Salt Lake City.
This Safilo-owned and operated facility employs 260 people, and cranks out over 2.5 million goggles each year, all under the Smith brand (with some Carrera brand goggles in the mix), in addition to hundreds of thousands of elite ballistic eyewear products for the military.
Smith’s proprietary sunwear and optical prescription program is based out of this facility, as well, in a notably modern lab staffed by optical experts.
One of my key takeaways was how remarkably clean and modern (more equipment infrastructure investment) this facility was. And, how the supremely competent work flow enhanced efficiencies in spades. One goggle = 2 days of lead time (with a supplied goggle frame). Yet another defining factor that clearly positions Safilo as a market leader. —EM
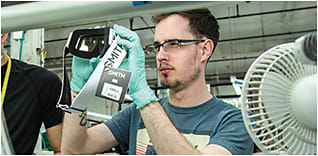
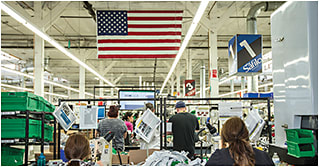
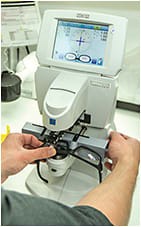
The Birth of a Frame
A purely product-centric process. Safilo delivers an impressive end-to-end production cycle, including everything from the first drawings through the handmade prototype, and onto the steps of production. Follow along here for a visual tour of the step-by-step process.
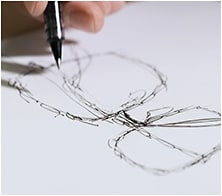
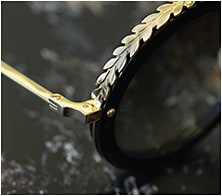
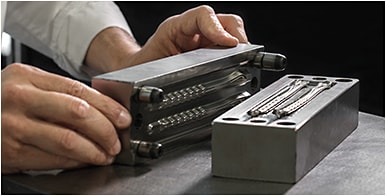
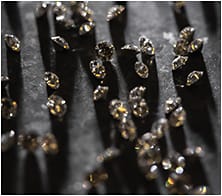
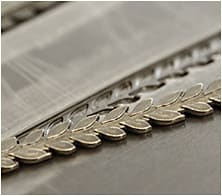
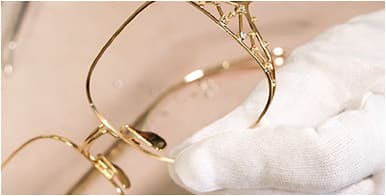
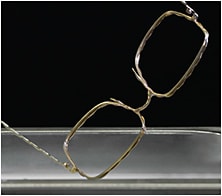
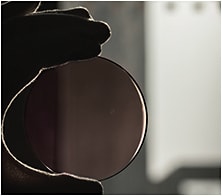
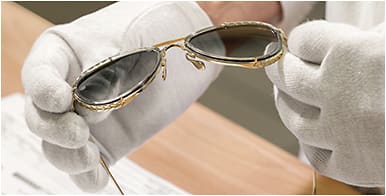
Did You Know?
In addition to a world-class design center at its headquarters in Padua, Italy, Safilo boasts U.S. design centers in Portland, OR, and New York City.